5 wichtigste Erkenntnisse aus über 50 Jahren Training in der Prozessanalyse
Die 5 wichtigsten Erkenntnisse aus über 50 Jahren Training in der Prozessanalyse
Tony Waters, Probeentnahmesystem-Experte, Ausbilder
Ein Probeentnahmesystem bei der Prozessanalyse ist eines der anspruchsvollsten Systeme in Ihrer Anlage. Nicht nur das Design ist diffizil, sondern auch der richtige Betrieb des Systems. Verändert man eine Einstellung nur minimal, kann dies einen erheblichen Effekt auf den gesamten Analyseprozess haben und erfordert eventuell eine viel größere Korrektur an einer anderen Stelle. Es ist daher nicht überraschend, wie viele detaillierte Fragen während der Process Analyzer Sampling System (PASS)-Schulungen von den Trainingsteilnehmer gestellt werden. In den letzten 50 Jahren meiner Lehrtätigkeit konnte ich zahlreiche Schulungsteilnehmer beobachten, bei denen während der Schulung buchstäblich ein Licht aufging. Die folgenden fünf Aussagen sind die wichtigsten Aha-Momente meiner Teilnehmer im Prozessanalyse-Systembereich.
„Die Zeitverzögerung ist oft länger als erwartet“
Die meisten Teilnehmer berücksichtigen nicht die Bedeutung der Zeitverzögerung in einem analytischen Messsystem und sind oft erstaunt, wie spät einige Analysemessungen in den Analysegeräten eingehen. Der Industriestandard für die Reaktionszeit liegt bei ca. einer Minute - von der Probeentnahme bis zum Messwert. Dieser kurze Zeitrahmen liefert nahezu Echtzeit-Messungen der Prozessbedingungen und Sie können fast unverzüglich Einstellungen vornehmen und den Produktabfall reduzieren.
In einigen Fällen kann es allerdings länger dauern, bis ein Messwert ausgegeben wird - auch wenn das Analysegerät nahe am Prozessanschluss angebracht ist. Diese Verzögerungen werden dann zum Problem, wenn sie die Erwartungen des Probeentnahme-Systemplaners überschreiten. Eine ungenaue Schätzung oder eine falsche Annahme zur Zeitverzögerung kann zu einer unzureichenden Prozesskontrolle führen.
Die Zeitverzögerung kann nur durch die Einstellung Ihres Systemdesigns reduziert werden. Unsere Schulung zu Prozessanalysegerät-Systemen umfasst eine praktische Übung, bei der wir die Zeitverzögerung in einem typischen Probeentnahmesystem berechnen. In der Übung hat unser ursprüngliches Design eine sehr lange Verzögerung von mehr als fünf Stunden. In diesem Beispiel können wir zeigen, dass wir diese Verzögerung nach einigen schnellen Systemänderungen auf den Industriestandard von einer Minute bringen können. Schulungsteilnehmer sind immer wieder von diesem Prozess begeistert und nehmen dieses Wissen dann mit in ihre Unternehmen.
„Meine Probe ist möglicherweise nicht typisch für die Prozessbedingungen“
Zeitverzögerung ist ein Problem, das unbedingt korrigiert werden muss, weil es den repräsentativen Charakter Ihrer Probe beeinflusst. Anders ausgedrückt, zeigt die Zeitverzögerung wie typisch die Probe für das Medium in der Prozessleitung zum Zeitpunkt der Analysegerätmessung ist. Beispiel: ein Prozessanalysegerätsystem mit einer Verzögerung von mindestens fünf Stunden. Wenn der Messwert negativ ist, korrigiert der Systembetreiber die Qualität und ist der Meinung, dass das Problem damit gelöst ist. Der Betreiber ist sich aber wahrscheinlich nicht bewusst, dass die Messung um mehr als fünf Stunden verzögert wurde. In diesem Zeitraum ist viel minderwertiges Produkt durch das System geflossen und wurde möglicherweise bereits an den Kunden ausgeliefert.
Auch wenn eine korrekte Probe entnommen und die Zeitverzögerung eingeschränkt wurde, kann es sich aufgrund Ihres Probeentnahmesystem-Designs um eine untypische Probe handeln. Zum Beispiel können Toträume im Prozessanalysesystem alte Samples auffangen, die sich dann mit einer neuen Probe vermenge und eine gemischte Probe schaffen, die nicht den Echtzeit-Prozessbedingungen entspricht.
Ihre Probe kann auch durch Lecks verschmutzt werden - nicht Lecks vom Probeentnahmesystem selbst, sondern Lecks, die aus der Umgebungsluft in das System führen. Sauerstoff kann zum Beispiel in ein System mit 100 Prozent Stickstoff bei einem Druck von 100 psig eintreten, weil der Partialdruck des Sauerstoffs an der Außenseite des Systems größer ist, als der Partialdruck im System. Diese Art von Leck kann durch die Erhöhung des Probeentnahmesystem-Partialdrucks vermieden werden, indem keine Umgebungsluft in das System eindringt.
„Ich muss mehr auf die Koaleszenzfilter achten"
Bei einer Schulung zur Probenahme sind die meisten Schulungsteilnehmer der Meinung, dass ein Koaleszenzfilter ein Gerät ist, das dazu verwendet wird, Flüssigkeiten von einer Gasprobe zu trennen und daraus zu entfernen. Das ist teilweise korrekt, gilt aber lediglich für Flüssigkeiten, die in Aerosolform vorliegen. Aerosol ist in zahlreichen Gasproben vorzufinden, weil Beschleunigungsvorrichtungen, wie Fliehkraft- oder Schwerkraftabscheider, Flüssigkeitströpfchen nicht voneinander trennen können. Ein Koaleszenzfilter in einem Probeentnahmesystem ermöglicht, dass die kleinen Tröpfchen zusammenkommen und sich zu großen Tropfen vereinen, die durch die Schwerkraft leichter zu trennen sind.
Unsere Teilnehmer sind jedes Mal überrascht, wenn ich ihnen erzähle, dass es zwei Bedingungen gibt, die einen Koaleszenzfilter ineffektiv machen. Zunächst fließt freie Flüssigkeit (d.h. Flüssigkeit, die noch nicht Aerosol-Form angenommen hat) aufgrund der massiven Größe der Flüssigkeitströpfchen mit sehr wenig Trennung durch einen Koaleszenzfilter. Zweitens: wenn die Durchflussrate durch einen Koaleszenzfilter zu hoch ist, werden die feinen Aerosoltröpfchen über die Koaleszenzfilterelemente hinaus gedrückt und nicht aus dem Durchflusspfad entfernt. Beide Szenarien erhöhen das Potenzial, dass Aerosoltröpfchen das Analysegerät erreichen und die Zuverlässigkeit Ihrer Messwerte reduzieren - damit wird der Koaleszenzfilter nutzlos.
„Das Verdampfen einer Flüssigkeit kann problematisch sein“
Viele Schulungsteilnehmer denken, dass die Verdampfung einer Flüssigkeit einfach ist. Doch dabei kann sehr viel schief gehen. Ziel ist es, eine Flüssigkeit unverzüglich in Dampf zu verwandeln, indem der Druck der Flüssigkeit schnell gesenkt wird. Aber anstatt die gesamte Probe schnell zu verdampfen, könnten Sie versehentlich durch Kombination von Verdampfung und Verdunstung eine fraktionierte Probe erzeugen. Wenn eine Probe fraktioniert, eignet sie sich nicht mehr zur Analyse.
In diesem Szenario verdunsten oft die leichteren Moleküle zuerst und bewegen sich zum Analysegerät hin, während die schwereren Moleküle in der flüssigen Phase zurückbleiben. Daher ist die Probe im Analysegerät nicht mehr länger repräsentativ für das Produkt, das der Produktleitung entnommen wurde. Wenn man versteht, was während der Verdampfung geschieht und erlernt, wie man mit Verdampfung in einem Analysesystem umgeht, kann dieses Problem in der Zukunft vermieden werden.
„Kondensation kann zum Problem werden, aber dieses Problem kann leicht gelöst werden“
Kondensation ist wahrscheinlich das häufigste Problem bei Gasproben. Teilnehmer meiner Schulungen sind oft überrascht, wie schnell Gase abkühlen (oder auch Flüssigkeiten). Umso mehr erstaunt es sie, wenn sie lernen, wie einfach man vorherbestimmen kann, wann es zur Kondensation kommt und mit welcher Temperatur die Kondensation gestoppt werden kann.
Denken Sie an ein System, das den Druck einer Gasprobe in einer Feldstation reduziert, die so nah wie möglich am Anschluss angebracht sein soll. Vergessen Sie nicht, dass fast alle Gase bei einem Druckabfall Wärme verlieren (dieses Phänomen ist als Joule-Thomson-Effekt bekannt). Wenn der Druckabfall nur gering ist, kann ein einfacher Druckminderungsregler verwendet werden, und die Sorge um Kondensation entfällt. Aber ein großer Gasdruckabfall löst aufgrund des enormen Wärmeverlusts eine starke Kondensation aus. Die Wahrscheinlichkeit, dass dies auftritt, erhöht sich, wenn das Gas nahe an der Taupunkttemperatur ist.
Das Design von Probeentnahmesystemen für die Prozessanalyse ist eine immerwährende Entdeckungsreise. Auch nach 50 Jahren im Umgang mit Probeentnahmesystemen lerne ich noch dazu - und auch ich habe noch so manchen Aha-Moment. Schulungen sind der Schlüssel, um Ihre Fähigkeiten zu erweitern und weitere Potentiale zu entdecken und entfalten. Auch in Ihrer täglichen Arbeit werden Sie eigene neue Erfahrungen sammeln, die zu genaueren und zuverlässigeren Prozessanalysesystem-Messwerten führen werden.
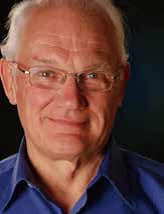
Informationen zum Autor
Tony Waters ist ein Industrieexperte und Berater für Swagelok. Er verfügt über mehr als 50 Jahre Erfahrung mit Prozessanalysegeräten und deren Probeentnahmesystemen, hat in der Technik und im Marketing für einen Hersteller von Analysegeräten, einem Endbenutzer und einem Systemintegrator gearbeitet. Er gründete drei Firmen, um der Prozessindustrie spezialisierte Dienstleistungen für Analysegeräte zu bieten und ist Experte für die Anwendung von Prozessanalysegeräten in Raffinerien und Chemiewerken.
Drei Regeln für präzise Analyseergebnisse
Erfahren Sie mehr über drei häufige Problemfelder in Probenahmesystemen, die zu ungenauen Analyseergebnissen führen und Sie zudem Zeit und Geld kosten.
Probeentnahmesysteme 8 häufige Probleme bei der Genauigkeit von Prozessanalysegeräten
Der Probeentnahmesystem-Experte und erfahrene Ausbilder Tony Waters bietet Betriebsleitern und Entwicklungsingenieuren bewährte Methoden zur Erkennung und Lösung von 8 häufigen Problemen bei der Genauigkeit von Prozessanalysegeräten.
Dampfwärmetauscher und Begleitheizungssystyeme: Bewährte Methoden für Konstruktionsingenieur
Bei der Entwicklung und Auswahl von Wärmetauschern und Begleitheizungen für individuelle Dampfsysteme ist es wichtig, dass Konstruktionsingenieur die Betriebsfunktionen und -anforderungen ihres jeweiligen Systems verstehen. Sehen Sie sich die bewährten Methoden an, um die Dampfwärmetauschersysteme in Ihrem Werk zu verbessern.